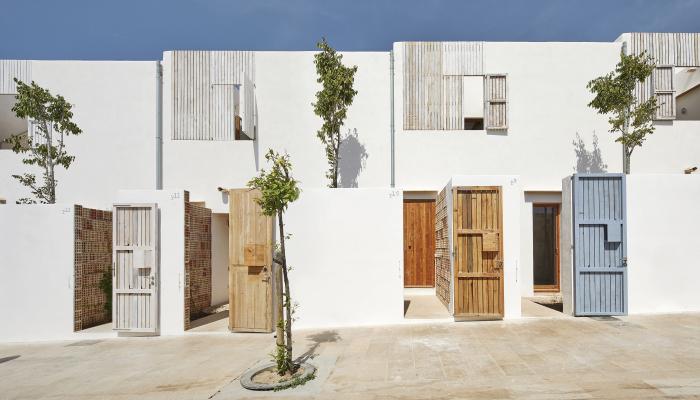
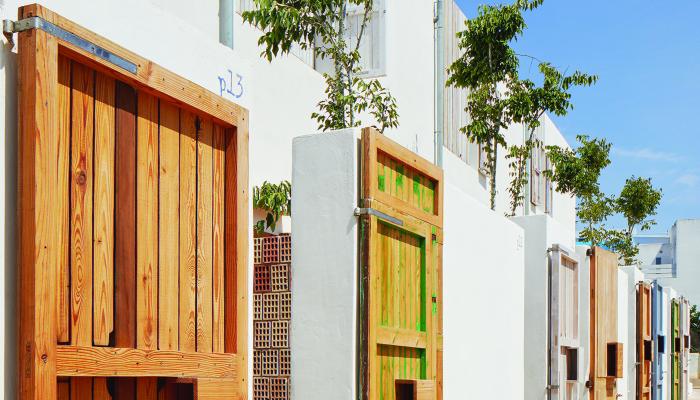
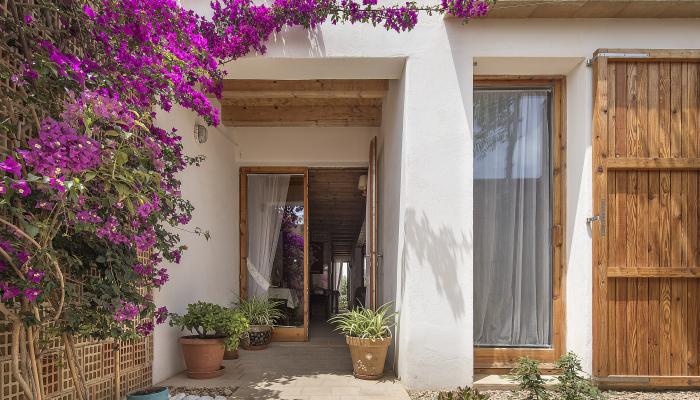

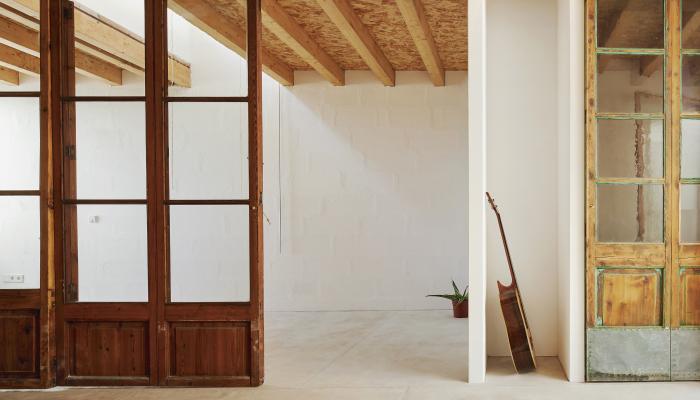
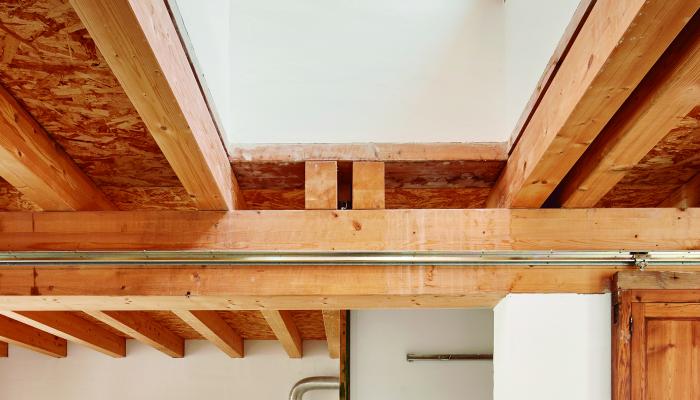
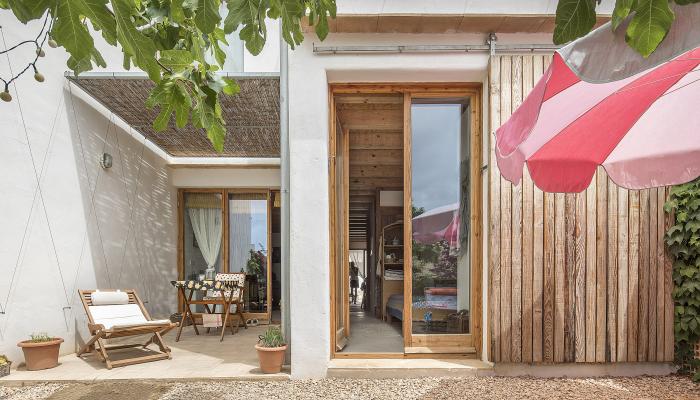
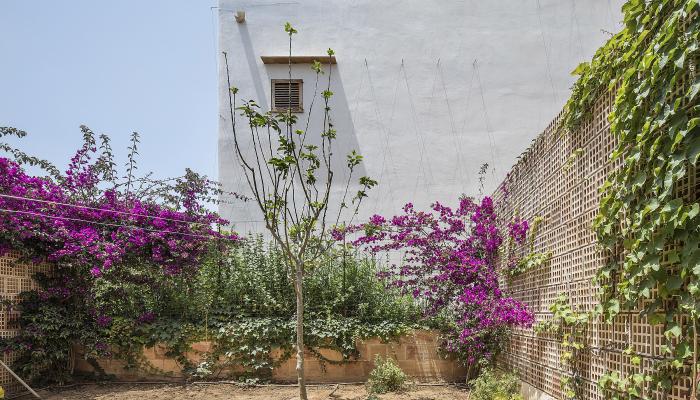
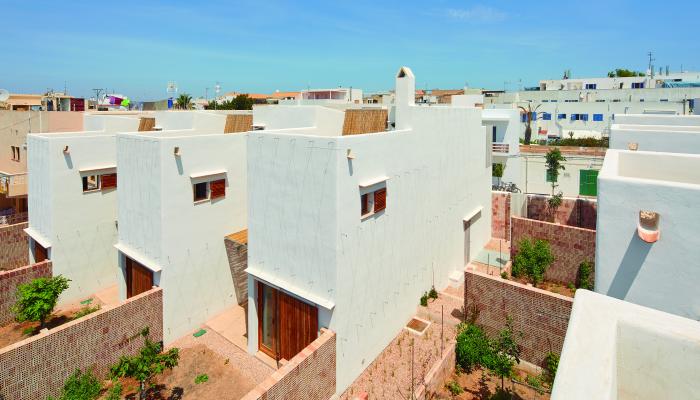
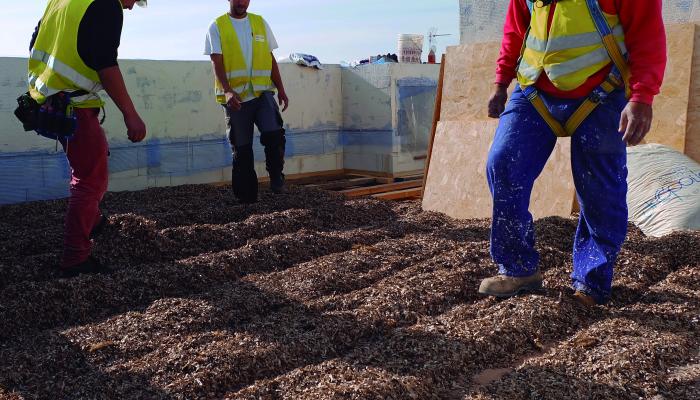

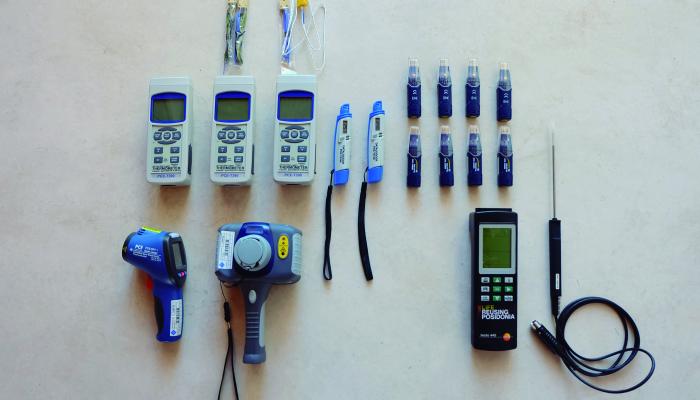
The project links heritage, architecture, and climate change through the construction of a prototype building consisting of 14 public housing units in Formentera, and its monitoring to assess the performance of local construction solutions and materials. The aim is to provide verified data on reducing environmental impact in the building sector.
The prototype demonstrates that the most sustainable construction systems—from an environmental, economic, and social perspective—are local, viable, and at risk of disappearing: artisan industries that produce organically, using raw materials sourced locally (km 0).
In this sense, the recovery of dry Posidonia oceanica as thermal insulation is particularly noteworthy. This solution, deeply rooted in traditional architecture, is promoted with the condition that its use is properly managed, reinforcing the idea that we do not simply inhabit a house, but rather, we inhabit an ecosystem.
In island territories such as the Balearic Islands, the fight against climate change takes on a dual dimension: in addition to sharing the global responsibility to combat climate change at the local level, these territories face a heightened vulnerability, making it a matter of survival. This, combined with the opportunities that islands present as potential laboratories, makes them well-suited to lead efforts in adapting to and mitigating the effects of climate change.
In this mission, rethinking the built environment—where people live, learn, and work—is essential, as approximately one-third of total energy consumption occurs in buildings, where ensuring adequate comfort and habitability conditions is crucial.
This project demonstrates that the Mediterranean climate and resources are well-suited to significantly reducing energy consumption both during the construction of housing and throughout its lifecycle. This, in turn, lowers CO₂ emissions and other pollutants associated with energy consumption, while also mitigating the social, economic, and environmental impacts of extracting, processing, and transporting fossil fuels from their place of origin.
Additionally, the project addresses another critical challange: integrating renewable energy generation within fragile and limited island territories. The land required for solar panels or wind turbines to meet energy demand can be significantly reduced by improving the efficiency of newly constructed and existing buildings.
The aim is to provide reliable data to the relevant administrations in the building sector to help reduce both the vulnerability of human environments to climate change and the collateral effects of current production and consumption models. In other words, to reduce resource consumption while enhancing comfort and habitability amid the current scenario of global temperature increase. At the project level, this translates into the following objectives:
Demonstrate the feasibility of using locally available materials traditionally employed before industrial development, such as Posidonia oceanica insulation and mass lime concrete as a structural solution, supported by the corresponding performance tests.
Reduce emissions and energy consumption, specifically:
-. 50% reduction in CO₂ emissions during the construction process (maximum threshold: 564,085 kg CO₂).
-. 75% reduction in useful energy consumption over the building's lifespan (maximum consumption: 15 kWh/m²/year).
-. 60% reduction in water consumption (maximum threshold: 88 l/person/day).
-. 50% reduction in waste production (maximum threshold: 35.18 tonnes).
Determine the average real unit cost of any multi-family housing development that meets the above requirements, ensuring an additional cost of less than 5% compared to equivalent developments that comply only with current regulations.
Promote and encourage the adoption of these principles in island architecture, ensuring their application contributes to both mitigating global temperature rise and adapting to climate change.
Traditional architecture is the constant reference for the Reusing Posidonia project, not in terms of form, but as a working methodology.
However, some of the basic materials of traditional construction are depleted, protected, or extremely scarce, and must be imported by ship, increasing consumption and energy expenditure. This particularly affects three types of materials:
Materials obtained from the island's sandstone quarries, now exhausted (Marès).
Straw harvested on the island, which is very scarce and primarily used for livestock.
Wood, which is practically non-existent, since the native junipers once used for building slabs are now protected.
Therefore, the availability of these materials is entirely dictated by Formentera’s insular conditions, making it necessary to use materials that can be sourced from the sea, such as:
Posidonia oceanica fibers, collected and dried on the island.
Construction pallet remnants, which remain on the island due to the high cost of shipping them back.
Quarry materials, transported by boat.
In response to this limitation, the project proposes an alternative for certain materials, such as Posidonia oceanica, redirecting the budget that would have been spent on their purchase and transport from outside the island toward hiring local, low-skilled labor for its collection, sun-drying, and subsequent compaction onto pallets to achieve 16 cm of roof insulation.
The product is completely organic, and the sea salt acts as a natural biocide, making it easy to use.
The remaining materials used in the project have been selected through a market study based on economic cost, embodied energy, and their suitability for the required comfort levels.
The use of natural materials, which are generally more fragile than industrialized ones, necessitates selecting the construction system at the earliest stage of the design process. This ensures that the organization of spaces and final execution decisions are informed by an understanding of the advantages and limitations of the materials.
By applying these construction criteria alongside a traditional building system adapted to the terrain, climate, and local customs, a prototype single-family house was built in two independent blocks, optimizing the availability of two street-facing facades. This arrangement maximizes the cooling potential of prevailing sea breezes in summer through passive design, as the homes feature dual orientation and cross-ventilation.
Its interior layout follows a Z-shaped configuration for the living/dining/kitchen area, with direct street access to preserve the traditional relationship of rural settlements and eliminate the need for elevators, communal spaces, and shared staircases.
Each home has dedicated outdoor areas: ground-floor units feature private gardens, while first-floor units have rooftop terraces accessed via private staircases.
The building has an A energy rating, with Posidonia oceanica insulation compacted at 185 kg/m³, forming a 16 cm thick roof layer.
The walls are composed of 25 cm thick aerated concrete, except for the north-facing walls, which are 30 cm thick. All glazing is low-emissivity. Windows exposed to solar radiation are shaded using porches, pergolas with vines and reeds, or Mallorcan shutters made of rot-resistant larch wood.
Cables have been installed on the facades to facilitate the growth of climbing plants, which shield the blind walls, reducing solar radiation by over 90% in covered areas.
In winter, passive air conditioning is supplemented by a centralized biomass boiler with 92% efficiency, which also heats domestic hot water (DHW) via heat exchangers, with individual consumption monitoring.
The size of all openings has been calculated to ensure direct sunlight exposure on the least favorable day of the winter solstice.
The first-floor homes have a dual-orientation skylight on the roof.
In winter, opening the south-facing blinds transforms them into a solar collector.
In summer, closing the blinds while opening the windows enables natural ventilation through the stack effect.
The measured indoor thermal comfort averages 21ºC in winter anda 26ºC in summer.
It is a climate change adaptation project promoted by the Balearic Housing Institute (IBAVI) and the Directorate General of Energy and Climate Change of the Balearic Islands.
This project enables the use of some natural materials typical of the island, along with other residual materials and/or those sourced from other locations, as well as the traditional and cultural construction methods typical of Formentera. A good example is the use of dry Posidonia oceanica as an insulation material, utilizing an abundant local waste with favorable insulating properties, avoiding the need to resort to foreign materials, and offering a new approach to building in both the public and private sectors.
This strengthens cultural tradition while promoting greater energy efficiency and the use of ecological technologies, increasing the competitiveness of the island's local production systems and helping to maintain, enhance, and care for the island's natural resources.
This results in a modern building that is respectful of the environment and cultural traditions of the island, offering maximum confort in modern, high- quality homes, where the characteristics of some natural materials and elements recovered from usable waste ar combined with construction systems and ecological, recycled, or optimized foreign materials, achieving the best market prices.
The LIFE Reusing Posidonia project was promoted by the Balearic Institute of Housing (IBAVI) and developed by its own Technical Architecture Team, comprising Antonio Martín Procopio, Joaquín Moyá Costa, and Alfonso Reina Ferragut, under the direction of Carles Oliver Barceló (Architect Director) and María Antònia Garcías (IBAVI Manager).
IBAVI is a public entity under the Ministry of Territory, Energy, and Mobility of the Autonomous Community of the Balearic Islands.
The project had the collaboration and co-financing of the Directorate General of Energy and Climate Change of the Autonomous Community of the Balearic Islands.
The materials used in the project have been chosen while always prioritizing, as far as possible, the use of products that are healthy, ecological, locally sourced (km 0), and economically viable.
In this sense, the extraction of the Posidonia oceanica material used has been limited exclusively to areas where the accumulation on beach sand exceeded the amount necessary to maintain the balance of the coastal dune ecosystem, taking maximum precautions to avoid any impact on it.
The following have been selected:
Reusable local waste, such as:
Reused wood from landfill
Aggregates from the construction site itself during the excavation phases or waste from aerated concrete blocks
Posidonia oceanica, dried and confined on pallets
Local organic products, such as:
Sandstone, for the structure (vaults)
Aerial lime made in Mallorca, fired using recycled oil, for exterior plaster
Sandstone slab and ceramic tile, fired in Moorish ovens fueled with biomass, for flooring
Ceramic blocks, fired in Moorish biomass ovens, for partitions
Clay, adobe, and ceramics fired with biomass
Non-local organic products, such as:
Laminated timber from Austria, PEFC-certified, for the structure (slabs)
Larch wood from the Basque Country, PEFC-certified, for exterior carpentry
Mass lime concrete, non-prefabricated, for the foundation
Polished lime slab finished in situ, for interior flooring
Recycled cotton panels, for acoustic insulation of interior partitions
Natural cork board, FSC-certified, for acoustic insulation of flooring
Wood protection based on vegetable raw materials, free of lead, heavy metals, or polyurethane
Silicate paint for walls and partitions
Recycled or optimized products, such as:
Aerated concrete block, with an environmental product declaration
Aerated concrete or metal profiles with recycled steel for the structure (walls)
EPDM waterproofing
Halogen-free and PVC-free electrical installation
- Plumbing. DHW, and greywater systems based on polyethylene and polypropylene
The project successfully addresses several fundamental factors, such as the viable use of natural materials as construction elements, the recycling and reuse of building resources and waste materials, which facilitate, improve, and optimize insulation and indoor climate comfort, as well as the reduction of emissions (carbon footprint) and energy and water consumption.
Insulation depends on the air bubble content indoors, so any local waste with a high air content could be a potential insulator. This is the case for the dried dead leaf of P. oceanica, used as a thermal insulator, as was done in traditional architecture.
Dead Posidonia benches are essential to preserve the beach sand during storms. However, in Formentera, their accumulation allows the use of the upper layers, with an annual usable volume of about 4,000 m³, which would allow any possible new construction on the island to be insulated.
To check its validity as insulation and determine the coefficient of thermal conductivity, different tests were carried out in collaboration with the University of the Balearic Islands (UIB). The result was a success, providing very good insulation when arranged in layers 16 cm thick, with a density of 185 kg/m³, at a rate of 20 kg/m². Once laid out, it was waterproofed with EPDM and protected with dry-mounted sandstone slabs.
Dried Posidonia is rot-proof and has no natural predators outside the marine environment, so its durability is unlimited under normal conditions of use, and it was used uninterruptedly in the traditional architecture of the Pityusic Islands until the beginning of the last century. Therefore, this solution could be applicable in all Mediterranean locations with Posidonia accumulations that allow its use.
The project reduced water consumption from 220 to 88 l/person/day, with an efficient design of the DHW installation and the location of the taps, placed less than 1 m from the hot water exchanger to avoid wasting cold water. Consumption was also reduced with water-saving mechanisms in the kitchen and bathrooms (pressure and flow reducers, taps with cold opening, etc.) and by installing 6 m³ rainwater cisterns under each terrace, which automatically irrigate the plants planted for bioclimatic purposes
Since the average rainfall regime is 345 l/m² per year, the system provides 450 l/day for irrigation during the three-month dry season. In addition, a greywater phytopurification plant was installed with a 17 m³ cistern, which regenerates shower water for reuse in the toilets, accounting for 20% of daily per-person water consumption. Likewise, drought-resistant plants with low water requirements and tolerant of the marine environment, typical of xeriscaping, were selected.
In terms of waste, the prototype built achieved a 50% reduction in waste production during construction, with a total volume of only 33.
At the level of emissions, all were calculated from the BEDEC construction database of the ITEC Institute of Construction Technology. The reduction finally achieved was 63.45%, exceeding the initially proposed target of a 50% reduction in CO2 emissions.
Finally, in terms of climatic comfort, the results obtained showed the good functioning of the insulation both in summer and winter, with constant reductions of 5 ºC in temperature with respect to the outside and 15 ºC with respect to surfaces exposed to direct sun in summer, and maintenance of the average indoor temperature of 15 ºC in winter. with an average time of 1 h to reach 21 ºC by air conditioning, with a relative humidity of more than 75%.
The project has received numerous awards and mentions, including:
BAM012 Award Finalist, Mediterranean Bioarchitecture
Finalist for the Endesa Awards for sustainable real estate development
FAD Architecture Award 2018
Spanish Architecture Award 2019
The total budget for the development of the project was €1,851,430.87, being financed by the European Union, which contributed 40.73% of the funds, and by the Balearic Institute of Housing (IBAVI) and the General Directorate of Energy and Climate Change of the Ministry of Territory, Energy and Mobility of the Government of the Balearic Islands, which contributed the remaining 59.27%.
Posidonia is a protected plant, whose use requires the authorization of the Species Protection Service of the Ministry of Environment and Territory.
Decree 25/2018, of 27 July, on the conservation of Posidonia oceanica in the Balearic Islands (BOIB no. 93 of 28 July 2018) contemplates preserving traditional uses, among others, as an insulator in traditional construction.
The project lasted approximately 59 months, taking place between August 1, 2013 and June 29, 2018.
Institut Balear de l’Habitatge (IBAVI). 2018. Life Reusing Posidonia. - After-Life Communication Plan. 8 pp.
Balearic Institute of Housing (IBAVI). 2018. Life Reusing Posidonia. - Layman Report. 13 p.p.
Oliver C.; Martín A.; Moyá, J. 2018. Life Reusing Posidonia. LIFE12 ENV/ES/000079. Institut Balear de l'Habitatge (IBAVI). 148 pp.
Carles Oliver Barceló
Director of the Life Reusing Posidonia Project
Balearic Institute of Housing (Ibavi)
C/ Manuel Azaña, 9 – 07006 Palma de Mallorca
Email: reusingposidonia@ibavi.caib.es
Telephone: 971 78 45 25 - 971 78 49 89